Ensuring optimal performance of lighting towers is not just about light; it’s about maximising productivity and ensuring a safe working environment. Here are six critical reasons why monitoring is key:
Location Matters: A lighting tower not positioned correctly at the start of a shift results in lost productivity. Efficiently track and manage locations to minimise downtime.
Fuel Assurance: Guarantee uninterrupted operations by monitoring fuel levels. Running out of fuel mid-shift is not only inconvenient but can significantly impact productivity.
Battery Health: Measure battery voltage to ensure your lighting tower starts when needed. Avoid unexpected downtime due to a dead battery and keep operations running smoothly.
Remote Diagnostics with Fault Codes: Identify and address issues remotely, preventing major breakdowns. Early detection means timely intervention and less disruption to your workflow.
Precise Servicing Schedules: Keep track of engine hours for accurate scheduling of maintenance. Proactive maintenance is key to preventing costly repairs and extending the life of your equipment.
Safety on Level Ground: Ensure the lighting tower operates on level ground to prevent dangerous situations on sloped surfaces.
Enjoy the benefits of monitoring through the Senquip Portal; typically free, with no ongoing hosting fees. Stay informed, stay productive, and prioritise safety with efficient lighting tower monitoring.
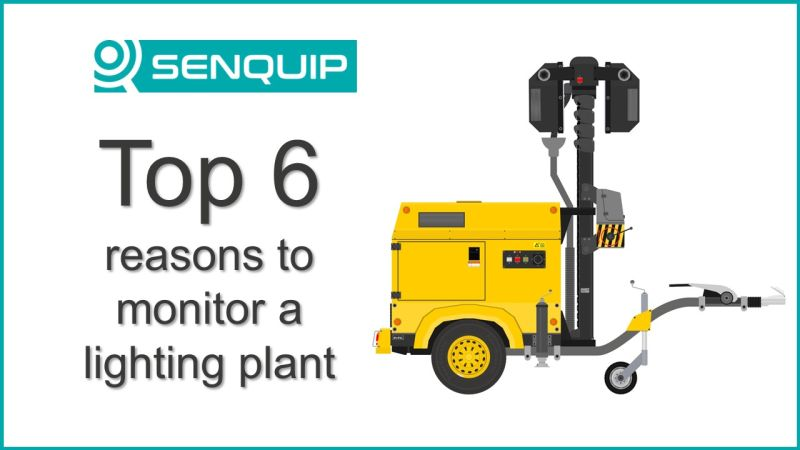