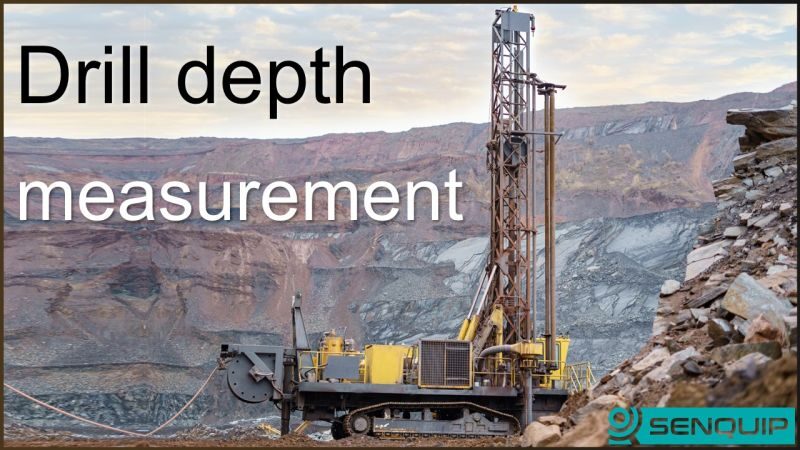
Real-time drill depth measurement is essential for optimising drilling operations. By accurately monitoring drill depth, operators can:
π’ Enhance Operational Efficiency: Ensure the drill bit operates at the correct speed and pressure for the formation, reducing equipment wear and minimizing downtime.
β° Improve Geological Data Collection: Accurately correlate geological data with specific depths, aiding in future exploration and production efforts.
π° Control Costs: Manage drilling costs effectively by avoiding unnecessary deviations and over-drilling.
Accurate drill depth can be calculated by knowing the drilled length and drill angle. While angle measurement is typically straightforward with an inclinometer, depth measurement involves more complexity. Here are some methods:
π Count Revolutions: Mount a rotary sensor connected to the centre of the feed motor.
β Count Teeth with Proximity Switches: Use two hall-effect or inductive proximity switches to count sprockets.
β Measure Chain Movement: Mount a geared sensor against the chain or use a spring-loaded friction wheel.
π Wireline Sensors: Measure drilled length with a steel wire running in a loop around a pulley wheel on the hammer rotation unit.
π Draw Wire Sensors: Register extension with a draw wire mounted to the feeder.
π Hydraulic Flow Meters: As a last resort, mount a flow meter into the hydraulic circuit of a cylinder feederβthough this is expensive and only applicable in certain systems.
The versatility and ruggedness of Senquip telemetry devices make them ideal for monitoring drill rigs.
For more information on drill depth sensors, contact Senquip distributor Macquarrie Corporation at sales@macquarrie.com.